1、引言
為滿足80萬噸重油催化裝置擴能需求,對煙氣輪機一軸流風機一電動(發(fā)電)機組簡稱三機組,同步進行了擴能設計。以利舊、節(jié)約和節(jié)能原則,確定了最優(yōu)的擴能設計方案。擴能設計后,軸流風機改造額定風量達到2050m3/min,出口壓力達到0.35MPa,配套額定功率9720kW的煙氣輪機。三機組夏季發(fā)電約500kW,冬季發(fā)電約900kW,能量回收效果顯著。
2、軸流風機擴能設計
2.1設計原則
2.1.1保證改造后軸流風機的安全性和可靠性
80萬噸/重油催化裝置配備主風機三臺,其中,軸流風機在三機組里與煙氣輪機同軸,一旦軸流風機停機,煙氣輪機將無法投用,裝置能耗將大幅上升。所以,軸流風機的安全性和可靠性尤為重要。原煙氣輪機額定功率8000kW,改造后的煙氣輪機額定功率9720kW,要求與煙氣輪機相聯(lián)接的聯(lián)軸器、軸流風機軸頭安全可靠。
2.1.2充分利用現(xiàn)有配置
為了最大限度減少改造工程量和降低改造費用,對原有設施、設備盡可能利用。
重油催化裝置三機組為同軸式,機組布置形式,如圖1所示。
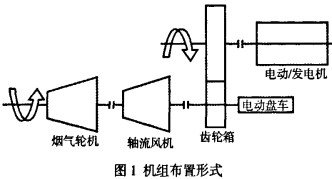
2.1.3保證改造后軸流風機的經濟性
三機組中的軸流風機是催化裝置中耗電最大的設備,額定軸功率8721kW,最大軸功率9695kW,軸流風機效率提高1%,一年就可以節(jié)省70萬度電,對降低能耗、提高經濟性有重要作用。
2.2改造內容
2.2.1軸流風機排氣側軸頭強度和鍵聯(lián)接強度校核計算
核算后的軸流風機轉子排氣端軸頭直徑由120mm增大到140mm;風量增加比較大,在轉子直徑不變的情況下,葉片高度和寬度等均增大,因此,整個轉子需要重新設計制造。
2.2.2內部構件改型設計
與轉子對應的內部構件重新設計制造。機殼、徑向軸承、推力軸承、軸承座、高壓平衡管道、排空管道及靜葉調節(jié)系統(tǒng)(含伺服馬達)等利舊。
2.2.3更換煙氣輪機一軸流風機膜片式聯(lián)軸器
在設計方案中,更換煙氣輪機一軸流風機膜片式聯(lián)軸器。采用備齒保安型金屬疊片撓性聯(lián)軸器,帶全密封護罩(帶呼吸帽及回油孔)。
(1)傳遞功率:11000kW;
(2)形式:膜片式;
(3)服務系數(shù):1.75。
2.2.4更換進氣過濾器
進氣過濾器設計要求如下:(l)過濾后含塵濃度≤(1.0-1.5)mg/m3; (2)過濾后含塵粒度≤(5—8)μm;(3)設計溫度:常溫;(4)設計初始壓差:(80~120)Pa;(5)設計報警壓差:350 Pa;(6)最大操作流量:2600 Nm3/min,
新更換的進氣過濾器是新型的4面進風過濾器,過濾面積大于原2面進風過濾器面積近l倍,過濾器初始壓差在( 50~100)Pa,降低了人口壓力損失。此外,新更換的進氣過濾器強化了結構合理性,延長了濾布的使用壽命,更換濾布操作也更加簡易可行。
2.2.5更換入口管道及整流柵
由于風量增加,為了減少管道阻力損失,入口管道直徑由1400mm改為1600mm.同時更換入口整流柵。
2.2.6取消進氣消音器
按設計,進氣消音器阻力損失為500 Pa,大于進氣過濾器的阻力損失,為了進一步降低入口壓力損失,取消了進氣消音器,在進氣管道進行外保溫,降低現(xiàn)場噪音。
3、擴能設計后軸流風機的技術規(guī)范
軸流風機擴能后的基礎數(shù)據和技術條件,如表1所示。

3.1軸流風機的技術指標
(1)流量調節(jié):全靜葉可調。
(2)進氣口要求:朝向:向下;聯(lián)接形式:法蘭;壓力等級:PN0.6:口徑:DN1200。
(3)排氣口要求:朝向:向下;聯(lián)接形式:法蘭;壓力等級:PN 1.6;口徑:DN800。
(4)機殼剖分形式:水平。
(5)多變效率:1P《89%(設計工況點)。
(6)設計壽命:20萬h(主機零部件)。
(7)設計滿負荷條件下連續(xù)運轉時間:≮3年。
(8)轉向(從煙氣輪機端看壓縮機):逆時針。
(9)靜葉可調:全部連續(xù)靜葉可調。
可調節(jié)級數(shù):16級
執(zhí)行機構:液壓
可調范圍:(22~79)°(起動角度:220)
(10)轉子部件:雙出軸
動平衡:高速動平衡(軸承箱振動≯1,8mm/s);轉子的超速試驗:至少在工作轉速的110%的轉速下進行,時間不少于1min。
(11)軸承形式及狀態(tài)監(jiān)測:
徑向軸承:橢圓瓦。徑向軸承內埋測溫元件2個,每個徑向軸承部位安裝2個(互成90。角)振動探頭。推力軸承:Kingsbury。
止推軸承主推力面內埋測溫元件2個,付推力面內埋測溫元件2個,采用鎧裝熱電阻(vrioo三線制鉑電阻)。推力軸承側安裝1個軸位移探頭(利舊)。
(12)軸流壓縮機的主要零部件材質:
主軸:25Cr2N14MoV;葉片:2Cr13;靜葉承缸:QT400-15;調節(jié)缸:Q235A鋼板焊接;導向環(huán)≯:35#。
3.2性能保證
(1)產品應保證表一中規(guī)定的流量、壓力等性能參數(shù)。
(2)主風機的主要零部件的設計壽命為20萬h。
(3)主風機在設計條件下連續(xù)運轉時間不少于3年。
(4)機械保證期為運轉12個月或交貨后18個月。
(5)主風機消耗功率公差:≯+4%。
4、軸流風機設計實施
軸流風機的拆卸和組裝規(guī)則:(1)拆除對輪罩,復查煙氣輪機一軸流風機、軸流風機一齒輪箱、齒輪箱一電動(發(fā)電)的同軸度;(2)拆除附屬管線;(3)拆卸壓縮機與變速器、煙機間的聯(lián)軸器;(4)檢查瓦間隙;(5)拆卸壓縮機進、出氣側軸承;(6)拆卸壓縮機機殼上、下部連接螺栓和定位銷釘;(7)吊起上機殼;(8)吊出靜葉承缸上部.吊出轉子;(9)再將驅動缸下部和靜葉環(huán)下部吊出分離;(10)檢查轉子圓跳動。轉子圓跳動檢查部位,如圖2所示。檢測數(shù)據及標準,如表2所示。
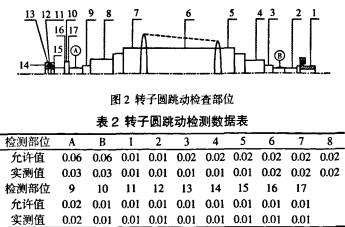
(11)檢查轉子位置。通過調整軸承瓦背墊片,調整轉子與殼體之間相對位置。檢查部位,如圖3所示。檢測數(shù)據,如表3所示。
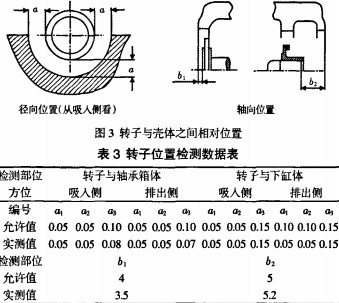
(12)轉子檢查后,裝上兩側軸承箱和支撐瓦,布好鉛絲,吊入轉子,用塞尺塞側間隙。并比較上下半所得值。緊固上承缸螺栓,測量葉片葉頂間隙。吊出上承缸,轉子,檢測出各部間隙值。葉頂間隙檢查,如圖4所示。檢測數(shù)據如表4所示。動葉頂間隙值范圍為(0.75~1.2)mm,靜葉頂間隙值范圍為(0.65~1.3 )mm。
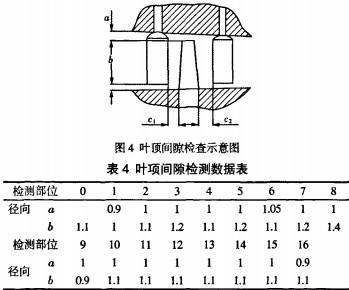
(13)用吊裝I具將驅動缸下部和靜葉環(huán)下部連接好,將靜葉承缸下部和驅動缸下部的組合體吊入下機殼。連好連接板,回裝靜葉承缸,緊固螺栓。回裝何服馬達。檢查靜葉安裝角度,位置應與伺服馬達行程指示—致。檢查合格后吊出上靜葉承缸,如圖5、表5所示。
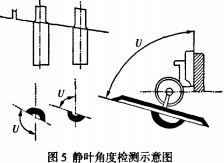
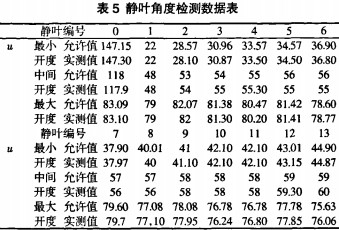
(14)檢查入口管線無異物后,回轉靜葉承缸,上機殼。緊固壓縮機機殼連接螺栓和定位銷釘。(15)回裝兩側上軸瓦,軸承箱蓋;匮b所有附屬管線,配合儀表探頭安裝,調校。(16)安裝各部聯(lián)軸節(jié)螺栓并做好記錄。
5、性能試驗
5.1空載試車
在設計轉速下連續(xù)運轉時間不小于4h。
機械試運轉應達到如下指標:(1)軸振動≯47μm; (2)軸位移≯04mm;(3)軸承溫度:徑向軸承≯80℃;推力軸承≯90℃。
5.2負荷試車
主風機的負荷試車應分檔次運行(按靜葉角度),負荷試運行應不少于72h,負荷試運中的技術指標為:(l)軸振動≯47μm;(2)軸位移≯0.4mm;(3)軸承溫度:徑向軸承≯80℃;推力軸承≯90℃。
5.3結果
在規(guī)定轉速和靜葉在最小工作角度下連續(xù)運轉4h和負荷試車72h,運轉合格。機械運轉和負荷試車最大軸位移0.25mm,小于Q4mm的標準要求;最大軸振動32μ,小于47μ的標準要求。最高軸承溫度82℃,小于90℃的標準要求;風量、風壓也達到設計要求。
6、結語
80萬噸重油催化裝置三機組擴能設汁后,軸流風機額定風量由原1600m3/min成功提高到2050m3/min;三機組常年發(fā)電(500~900)kW,最大1000kW。三機組自投用以來,機組振動、軸承溫度均在標準之內,從未發(fā)生過因機組故障導致的停機。
改造后的三機組在運行出力達到設計要求,運行平穩(wěn),滿足工藝要求,經濟及社會效益顯著。