對輥擠壓顆粒機是密閉鼓風爐煉銅、豎罐煉鋅以及密閉鼓風爐煉鉛鋅浮渣和各種含鋅中間返回料處理的一種重要設備。近年來為滿足顆粒質量的要求和提高造粒的操作可靠性,造粒機的性能和結構一直在不斷改進與完善。同時,為擴大造粒機處理各種原料的適應性,又在冷壓造粒的基礎上,發(fā)展熱壓造粒技術。而由于高溫、高壓造粒的采用,不僅需要選擇和開發(fā)相應的高強度、耐磨和低摩擦阻力的材質,還必須在輥子結構上采取易于更換的相應措施,從而對造粒機的設計和制造提出了更嚴格的要求。
近年來在輥子設計上采用的液壓支承裝置,可使輥子保持適合的成型壓力,在過負荷及過異物時起保護作用。此外,新采用的還有全封閉、高負荷容量的輥子軸承以及為主傳動專門設計的并可自行潤滑的減速機等。而減速機輸出軸與輥子軸又多以撓性聯(lián)軸節(jié)相連接,這樣當移動輥子后退時,可避免對主傳動裝置產生干涉。
低壓造粒機通常借助于上方料斗中粉料的自重給料,并由插板閘門控制給料量,而高壓造粒機則采用立式圓錐狀螺旋強制給料,螺旋形狀根據(jù)給料量和成型壓力而確定。給料螺旋通過無級調速裝置單獨驅動。
應該指出,影響顆粒質量的因素很多。由于原料水分、粒度分布的變動,螺旋的給料量及棍子的咬入點位置也隨之變化。為使成型壓力一定,并最終保持團塊強度,需及時調節(jié)給料同時檢測軸承的負荷力,使負荷力保持恒定,并自動調節(jié)螺旋轉速,實現(xiàn)給料裝置自動控制。
8、壓片機
壓片機是借助于偏心曲軸驅使下的上下沖頭在壓模內進行相對運動來完成壓粒過程的,有單沖頭壓粒機和轉盤式壓粒機兩種。日前單沖頭壓片機的最大生產能力為每分鐘200片,而轉盤式壓片機可高達每分鐘10000片左右。轉盤式壓片機要求原料有很好的流動性和黏結性一般情況下需要添加黏結劑和潤滑劑等輔助材料。
9、對輥式壓片機
對輥式壓片機主要由兩個等速相對轉動的輥子組成,原料在螺旋給料機的推送下被強制壓入輥子的縫隙中,隨著輥子轉動,原料逐漸接近輥子間最狹窄部位,得到片狀產品,再將其破碎篩分便可獲得各種粒度不規(guī)則的顆粒。該設備生產的顆粒形狀可靈活調節(jié)且處理量大,可達每小時數(shù)十噸。大部分粉狀物料都能采用這種這種方法進行造粒,并可以獲得多種形狀的顆粒制品。其缺點是顆粒表面不如壓粒機所制的顆粒完整。顆粒過于堅硬,對于要求復水后迅速分散的物料并不適合。主要的生產成本是輥子的磨損、更換和能量消耗。
10、攪拌混合造粒機
將粉料和粘結劑放入一個容器內,利用高速旋轉的攪拌器的攪拌作用迅速完成混合并制成顆粒的方法稱為攪拌混合造粒。它是在攪拌漿的作用下,使物料混合、翻動、分散甩向器壁后向上運動,并在切割刀的作用下將大顆粒破碎、切割。并和攪拌槳的作用相呼應,使物料得到強人的擠壓、滾動而形成致密而均勻的顆粒。由此可見,其微核生成和長大的機理與滾動造粒相似,只是顆粒長大的過程不是在重力或離心力作用下自動滾動,而是通過攪拌器驅使微粒粒在無規(guī)則的翻滾中完成聚并和包層。在攪拌混合造粒機中,部分結合力弱曲大顆粒被攪拌器或切割刀打碎,碎片又作為核心顆粒經過包層進一步增大。隨著物料從給料端向排料端的移動,顆粒增大破碎的動態(tài)平衡逐漸趨于穩(wěn)定。
常用的攪拌混合造粒機如圖1- 22所示。其構造主要由容器、攪拌槳、切割刀組成。操作時先將粉料倒人容器中,蓋上蓋,先把物料攪拌混合均勻后加入黏結劑,攪拌造粒。完成造粒后傾出濕顆粒或安裝于容器底部的出料口自動放出濕顆粒,然后進行干燥。
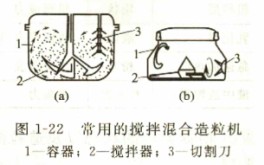
攪拌混合造粒是在一個容器內進行混合、捏合和造粒,與傳統(tǒng)的擠出造粒相比具有省工序、操作簡單、快速等優(yōu)點。該方法處理量大,造粒又是在密閉容器中進行,工作環(huán)境好,所以多應用于礦粉和復合肥料的造粒過程。另外,改變攪拌槳的結構、調節(jié)黏結劑的用量及操作時間可制備致密、強度高的顆粒,也可以制備松軟的顆粒。但所制備顆粒的粒度均勻性、球形度等不及滾動造粒。該設備的另一個缺點是不能進行干燥。為了克服這個弱點,研制了帶干燥功能的攪拌混合造粒機,即在攪拌混合造粒機的底部開孔,物料完成造粒后通熱風進行干燥,可節(jié)省人力、物力,減少人與物料接觸的機會。
三門峽富通新能源科技有有限公司主要生產顆粒機、秸稈顆粒機、木屑顆粒機、秸稈壓塊機等生物質燃料成型機械設備。