1、螺旋擠壓式成型顆粒機的種類
按螺旋桿的數(shù)量可分為單螺旋桿式、雙螺旋桿式和多螺旋桿式成型顆粒機。單螺旋桿式使用得較多;雙螺旋桿式成型顆粒機采用的是2個相互嚙合的變螺距螺旋桿,成型套筒為“8”字形結(jié)構(gòu)。雙螺旋桿式和多螺旋桿式因結(jié)構(gòu)復(fù)雜在生物質(zhì)成型顆粒機上應(yīng)用較少,主要用在其他物料的成型加工。
按螺旋桿螺距的變化不同可分為等螺距螺旋桿式和變螺距螺旋桿式成型顆粒機。采用變螺距螺旋桿,可以縮短成型套筒的長度。但螺旋桿制造工藝復(fù)雜,成本高。
按成型產(chǎn)品的截面形狀可分為空心圓形和空心多邊形(四方、五方、六方等)成型顆粒機。通過在螺旋桿的末端設(shè)置一段圓形截面的錐狀長度,可使成型后的成型顆粒燃料中心呈空心狀。通過改變螺旋桿成型套筒內(nèi)壁的截面形狀,可以使成型顆粒燃料的表面形狀呈四方、五方、六方等形狀。
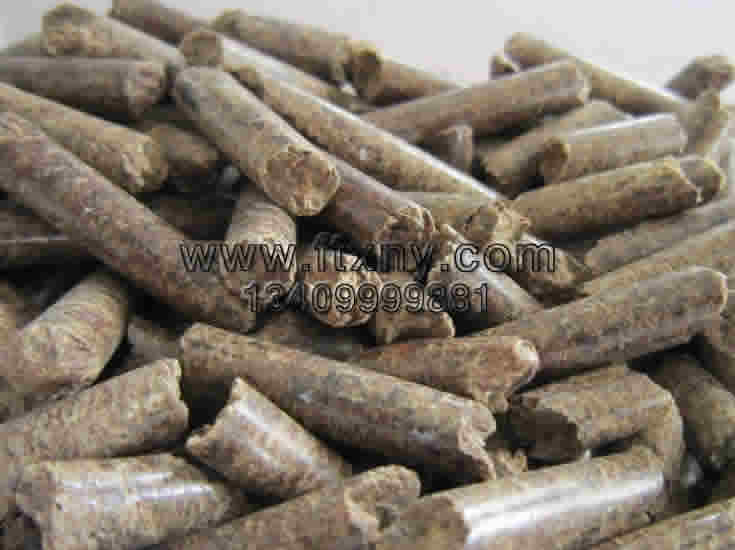
螺旋擠壓式生物質(zhì)成型顆粒機主要由電動機、傳動部分、進料機構(gòu)、螺旋桿、成型套筒和電熱控制等幾部分組成,其中螺旋桿和成型套筒為主要工作部件。
工作時,收集通過切碎或粉碎的生物質(zhì)原料,由上料機、皮帶輸送機或人工將原料均勻送到成型顆粒機上方的進料斗中,經(jīng)進料預(yù)壓后沿螺旋桿直徑方向進入螺旋桿前端的螺旋槽中,在螺旋桿的連續(xù)轉(zhuǎn)動推擠和高溫高壓作用下,將生物質(zhì)原料擠壓成一定的密度,從成型套筒和保型筒內(nèi)排出即成一定形狀的燃料產(chǎn)品。
3、主要工作部件
(1)螺旋桿
1)螺旋桿的結(jié)構(gòu)
在成型過程中,生物質(zhì)原料的輸送和壓縮是由螺旋桿和成型套筒配合完成的。螺旋桿的結(jié)構(gòu)形狀與幾何尺寸對原料的成型有很大的影響,在螺旋桿的全長上分為進料段和壓縮段,進料段通常采用圓柱形等螺距螺旋;壓縮段通常采用具有一定錐度的等螺距或變螺距的螺旋。螺旋桿的壓縮段是在較高溫度和高壓力下工作,螺旋桿與物料始終處于干摩擦狀態(tài),這就是導(dǎo)致螺旋桿磨損速度非?斓闹饕。
2)螺旋桿的磨損
當螺旋桿磨損到一定程度時,螺旋葉片頂部直徑變小,葉片厚度變薄,高度減小,螺旋桿與成型套筒配合間隙增大,產(chǎn)生的擠壓力變小,有時物料還會從螺旋桿與成型套筒的大間隙中反噴至進料口,致使成型速度變慢,生產(chǎn)率降低,成型效果變差。螺旋桿磨損嚴重時,還會造成擠不出料,出現(xiàn)“放炮”現(xiàn)象,甚至折斷螺旋桿。
3)螺旋桿減磨措施
在螺旋桿的壓縮段即螺旋桿頭部最后一圈螺旋葉片承受的壓力最大,磨損也最為嚴重,只要解決了這部分的磨損,整個螺旋桿的磨損問題也就解決了。變螺距螺旋桿因制造工藝復(fù)雜,成本高而很少使用。等螺距螺旋桿在成型過程中也主要是最前端的一個螺距起壓縮作用而磨損嚴重,為了延長使用壽命,解決螺旋桿頭部磨損嚴重的問題,第一種方法是對螺旋桿頭進行局部熱處理,使其表面硬化。例如,采用噴焊鎢鈷合金、堆焊618或炭化鎢焊條堆焊、局部炭化鎢噴涂或局部滲硼處理以及振動堆焊等方法對螺旋桿磨損嚴重部位進行強化處理。但通過這些方法進行處理后螺旋桿的使用壽命并沒有得到有效提高,且成本高,用戶很難接受。第二種方法是把磨損最嚴重的螺旋桿前部用耐磨材料做成可拆卸的活動螺旋頭,磨損后僅更換活動螺旋頭,螺旋本體還可繼續(xù)使用。第三種方法是螺旋桿頭部最后的一圈螺旋葉片的形狀向軸根部逐漸收縮,以便使這種壓力由后部的葉片承擔一部分。除此之外,后部的螺旋槽內(nèi)也應(yīng)堆焊耐磨材料,使葉片與螺旋桿之間有較大的過渡圓角,以增強這部分葉片的強度和耐磨性。螺旋桿的長度不宜太長和太短,以螺旋桿直徑76 mm為例,螺旋桿長度以350mm左右右為宜。螺旋桿頭部沒有螺旋的光軸部分長度應(yīng)根據(jù)原料的種類和成型顆粒燃料的要求來確定,它的作用是使成型后的燃料棒呈空心狀,通常成型木屑類原料選短一些,成型秸稈類原料或成型后需炭化的燃料可適當選長一些。
(2)成型套筒
1)成型套筒的結(jié)構(gòu)
成型套筒(前端)與螺旋桿之間應(yīng)有良好的尺寸配合,由于螺旋桿的安裝是采用懸臂軸的形式,因此這種尺寸配合應(yīng)保證螺旋桿在旋轉(zhuǎn)時不能與成型套筒內(nèi)壁相碰為宜。生物質(zhì)原料在成型擠壓推進過程中,主要是靠螺旋桿的轉(zhuǎn)動推進生物質(zhì)逐層成型的,螺旋桿的前段和頭部在整個推擠過程中與生物質(zhì)之間做高速相對運動,增加了單位產(chǎn)品的能耗。由于生物質(zhì)原料自身的特性和螺旋桿產(chǎn)生的綜合作用力(軸向、徑向和切向)會使一部分物料黏附在螺旋桿葉道內(nèi)或成型套筒內(nèi)壁上形成黏滯物,黏滯物的運動與螺旋桿以及成型套筒內(nèi)壁之間產(chǎn)生了摩擦,這兩種摩擦所產(chǎn)生的摩擦力都可以分解為軸向摩擦力和切向摩擦力。為防止黏滯物在成型套筒內(nèi)只隨螺旋桿轉(zhuǎn)動而不推料,必須增加物料與成型套筒內(nèi)壁的切向摩擦阻力和減少軸向摩擦阻力,因此,在成型套筒內(nèi)壁開有若干個縱向溝槽。成型套筒內(nèi)壁最佳的溝槽結(jié)構(gòu)形式、數(shù)量以及長度應(yīng)根據(jù)螺旋桿的結(jié)構(gòu)形式、成型的生物質(zhì)原料種類與物理特性,以及螺旋桿的轉(zhuǎn)速等實際情況來確定。
成型套筒的前端與螺旋桿配合工作,套筒內(nèi)壁呈一定錐度,成型套筒中后段內(nèi)壁的截面尺寸基本恒定,除對成型顆粒燃料起保壓保型作用外,也是成型顆粒燃料的出口,它決定了成型后成型顆粒燃料的外部形狀。螺旋桿擠壓成型后成型顆粒燃料的外部形狀除了圓形以外,還有四方、六方等多種形狀。
2)成型套筒減磨措施
成型套筒的材料采用較多的是45號鋼、球墨鑄鐵和各種耐磨合金材料。為延長成型套筒的使用壽命,可采取以下措施:①成型套筒的保型段加工成可調(diào)結(jié)構(gòu)'通過調(diào)整保型筒出口直徑的大小達到調(diào)節(jié)成型阻力的目的,保證成型所需的壓力,延長套筒的使用壽命,這種結(jié)構(gòu)在活塞沖壓式成型顆粒機的保型筒上應(yīng)用最多;②在成型套筒內(nèi)壁壓50進行局部耐磨材料噴涂,提高耐磨性能,延長使用壽命;成型套筒與進料套筒連接時,在壓緊圈內(nèi)加若干個A型和B型薄墊圈,待成型套筒壓縮段磨損到不能正常工作時,取下一個A型墊圈,增添一個B型墊圈,相當于成型套筒壓縮區(qū)前移了一個墊圈厚度的距離,繼續(xù)保持與螺旋桿的間隙,相應(yīng)延長了成型套筒的使用時間;④成型套筒磨損最快的錐形筒部分采用拆分方法進行加工,做成的活動耐磨襯套鑲嵌在成型套筒壓縮段,錐形筒磨損后可單獨拆換,套筒中后段作保型筒使用。
這樣一來,成型顆粒機使用一段時間需更換磨損件時,只需更換螺旋桿頭和錐形筒部分即可,不必將整體螺旋桿和整體成型套筒全部更換,可節(jié)省部分維修費用,充分延長螺旋桿主體和成型套筒保型筒的使用壽命,從而降低生物質(zhì)成型顆粒燃料的成型成本。
(3)加熱裝置
加熱裝置的一個主要作用是用于成型顆粒機啟動時的預(yù)熱。螺旋式生物質(zhì)成型顆粒機的加熱方式有多種,分外部加熱和內(nèi)部加熱、電加熱和蒸汽加熱,所用的加熱裝置的結(jié)構(gòu)形式也很多,如電熱管式加熱圈、筒式加熱圈、鑄鋁加熱圈等。
對加熱裝置的一般要求是:有一定的加熱功率,加熱速度快,加熱溫度可調(diào),保溫性能好,安全可靠,使用壽命長。中小型成型顆粒機大都采用外部加熱的方式,大型成型顆粒機多采用內(nèi)部加熱或蒸汽加熱方式。
穩(wěn)定成型溫度是加熱裝置的另一個主要作用。螺旋式生物質(zhì)成型顆粒機成型加工時,螺旋桿與原料、原料與成型套筒之間會產(chǎn)生大量的摩擦熱,使成型部件和成型原料升高一定的溫度,這一溫度很難維持正常成型。若沒有外部熱源輔助加熱,會造成冷機啟動困難,正常成型難以保證所需的木質(zhì)素軟化溫度,增加成型顆粒機的耗能和成型部件的磨損。
4、性能特點
螺旋擠壓式成型顆粒機的主要優(yōu)點是:結(jié)構(gòu)簡單,操作方便,體積小,占地少,機器產(chǎn)品價格低,對木屑類生物質(zhì)原料成型效果較好,可得到空心截面棒狀或多邊形狀的成型顆粒燃料產(chǎn)品,非常適合制作炭化燃料。缺點是螺旋桿和成型套筒的磨損速度較快,使用壽命都較低,單位產(chǎn)品能耗較高,高達125 kW·h/t,對農(nóng)作物秸稈類的生物質(zhì)原料成型效果較差,經(jīng)濟效益不突出;設(shè)備配套性能差,自動化程度較低等,難以形成規(guī)模效益,不便于大規(guī)模商業(yè)化利用。所以目前螺旋擠壓式成型顆粒機成型加工后的各種棒狀燃料產(chǎn)品主要還是用來制作機制木炭,以滿足農(nóng)業(yè)、畜牧業(yè)、冶金、環(huán)保、工廠、實驗、飯店、民用燒烤等需求,如圖6. 52所示。
4、大直徑螺旋擠壓式成型顆粒機
大直徑螺旋桿由于螺旋桿直徑較大,在轉(zhuǎn)速一定的條件下,進料量和推進速度都比較快,產(chǎn)生的阻力更大,對成型正常的生物質(zhì)原料螺旋桿的磨損速度會更快。因此,大直徑螺旋擠壓式成型顆粒機動力消耗大,主要磨損件的使用壽命低,對原料的適應(yīng)性較差,但生產(chǎn)率高,可實現(xiàn)多孔出料,結(jié)構(gòu)簡單,設(shè)備費用低。
為提高大直徑螺旋式成型顆粒機對原料的適應(yīng)性,延長主要磨損件的使用壽命,降低能量消耗。目前市場上的大直徑螺旋式成型顆粒機大都用于以“熟料”為主的生物質(zhì)原料的成型。生物質(zhì)原料經(jīng)過噴灑某種添加劑、發(fā)酵、過腹、提取加工后,原料中的木質(zhì)素、纖維素已經(jīng)軟化,機械特性(抗壓強度、韌性、硬度、彈性等)顯著降低,內(nèi)部的粗纖維等成分已經(jīng)發(fā)生變化,且添加成分分布均勻,生物質(zhì)的顆粒色澤變深,表面柔滑,成為“熟料”。擠壓成型這類生物質(zhì)時基本上能彌補各類成型顆粒機的主要缺陷,采用大直徑螺旋式擠壓成型顆粒機恰好能發(fā)揮自身的優(yōu)勢,可大大提高成型效率,有效地降低成型過程的阻力和成型能耗,延長螺旋桿和成型套筒的使用壽命。
大直徑螺旋擠壓式成型顆粒機對牛糞、糠醛渣、醋渣、酒渣、菇類基質(zhì)等生物質(zhì)“熟料”有很好的成型效果?煽焖賹⑴<S擠壓成燃料棒,解決糞便污染問題,圖6. 53所示的是大直徑螺旋擠壓式成型顆粒機外形圖,除能對上述原料進行成型加工外,還用于以煤粉、煤泥為主要成分的煤棒、煤塊、煤顆粒燃料的成型加工。
6、主要技術(shù)性能與特征
螺旋擠壓式成型顆粒機的主要技術(shù)性能與特征參考范圍見下表。
技術(shù)性能與特征 | 參考范圍 | 說明 |
要求原料粒度/mm | 3~5 | 生物質(zhì)原料的粒度越細小,越利于成型,但會劇增粉碎耗能 |
原料含水率/% | 8~12 | 生物質(zhì)原料的含水率過高或過低成型效果都會變差 |
產(chǎn)品直徑/mm | 50~70 | 產(chǎn)品呈空心棒狀居多,大螺旋、多孔成型“熟料”直徑較小,形狀為實心棒狀 |
產(chǎn)品密度/(g/mm3) | 1.1~1.4 | 密度太小,炭化后的炭棒易開裂,密度太大,會使成型耗能劇增 |
生產(chǎn)率/(t/h) | 0.2~0.5 | 一般生產(chǎn)率較低,大螺旋、多孔成型機的生產(chǎn)率較高 |
單位產(chǎn)品能耗/(kw·h/t) | >100 | 螺旋擠壓式成型能耗一直較高,“熟料”成型能耗可大大降低 |
螺旋桿的轉(zhuǎn)速/(r/min) | 300~350 | 螺旋桿的轉(zhuǎn)速不宜太高,否則成型耗能劇增 |
螺旋桿使用壽命/h | 50~80 | 一般材料的螺旋桿使用壽命較低,“熟料”成型使用壽命可大大提高 |
成型套筒使用壽命/h | 200~300 | 成型套筒的使用壽命一般是螺旋桿使用壽命的3~5倍 |
成型方式 | 熱壓成型 | 一般采用外部加熱,熱壓成型可減小成型阻力,降低成型能耗 |
動力傳動形式 | V型帶 | V形帶傳動采用居多,螺旋軸前增加一級齒輪傳動可增加擠壓力,避免卡死現(xiàn)象 |
對原料的適應(yīng)性 | 木屑類 | 螺旋擠壓式成型機對木屑類成型效果好,大直徑螺旋式成型機適合成型“熟料” |