由于高錳鋼( Mn13)耐磨,沖擊韌性高而廣泛用于選礦球磨機(jī)襯板易損件。目前,國(guó)內(nèi)外研究應(yīng)用表明,在高錳鋼件中添加強(qiáng)碳化物形成元素,使高錳鋼合金化及采用彌散硬化熱處理新工藝,是提高其耐磨性的有效途徑。但是加入合金元素,勢(shì)必增加生產(chǎn)成本,復(fù)雜的彌散硬化熱處理工藝在大生產(chǎn)中也難以控制,為此,采用了在高錳鋼中添加成本相對(duì)較低的鉻、稀土元素,產(chǎn)根據(jù)生產(chǎn)實(shí)際情況,制定了較為簡(jiǎn)便的彌散硬化熱處理新工藝,從而研制出“GML”新材料。實(shí)現(xiàn)了提高4#球磨機(jī)襯板的耐磨性,降低選礦成本的目標(biāo)。
2、襯板新材料的研制
研制新材料確定的化學(xué)元素成分見(jiàn)表1。

化學(xué)成分中碳與合金元素的配比為:
(1)影響高錳鋼耐磨性的主要因素是碳元素與錳元素的合理配比。碳含量低,鋼經(jīng)熱處理后,沖擊硬度低,耐磨性較差,碳量過(guò)高,熱處理后晶界極易形成粗大網(wǎng)狀碳化物,致使鋼的脆性增大,耐磨性也差。如果錳元素含量高,熱處理后硬度高,成本也高。如果適當(dāng)降低錳含量和碳含量,使錳碳比達(dá)到8~9的最佳配比,熱處理后不僅硬度提高,耐磨性也可提高。
(3)合金元素釩、鈦、鉻、鉬、稀土等,都是強(qiáng)碳化物形成元素,這些元素在高錳鋼中形成的特殊碳化韌是提高鋼耐磨性的關(guān)鍵,尤其是形成彌散狀的碳化物顯著提高鋼的耐磨性,但由于釩、鈦、鉬都比較貴重,所以選擇了又經(jīng)濟(jì)又能提高耐磨性的強(qiáng)碳化物元素,鉻和稀土首選元素。如果當(dāng)鋼中的合金元素含量較低時(shí),只能形成Fe3C普通滲碳體,所以只有在錳鉻元素與碳達(dá)到一定比值(約為1.8)時(shí)才能產(chǎn)生彌散狀的特殊碳化物(Cr7C2或Cr23 C8等),從而可顯著提高鋼的耐磨性。
彌散硬化熱處理工藝的確定。試制的4種彌散硬化熱處理工藝模擬方案見(jiàn)表2。
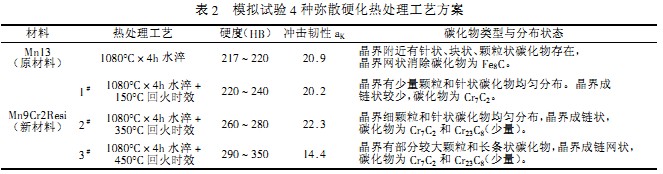
模擬試驗(yàn)4種處理工藝方案后,機(jī)械性能和金相組織顯示:2#型熱處理彌散工藝:1080℃×4h水淬后,在350℃回火時(shí)效后,其碳化物在晶界以細(xì)顆粒和細(xì)針狀均勻分布,界面成鏈狀其碳化物達(dá)到彌散分布,從機(jī)械性能方面看,硬度也較高,沖擊韌性也較高,比150℃回火時(shí)效工藝有較好的強(qiáng)度、硬度和韌性。450℃回火量效工藝其碳化物盡管也達(dá)到彌散分布,但晶界附近出現(xiàn)大塊鏈網(wǎng)狀碳化物,這樣鋼的脆性變大,對(duì)耐磨性是不利的。
3、新材料襯板的試用效果
1999年7月10日前試制出83件約重16t4#球磨機(jī)通體部新材料(Mn9Cr2Resi)襯板,并于1999年7月22日安裝于選礦4#球磨機(jī),易磨損的通體進(jìn)粒端,歷時(shí)10.5個(gè)月生產(chǎn)試用,于2000年6月9日磨損失效卸機(jī),共處理磨選原礦75.9萬(wàn)t,與原型襯板(Mn13)處理磨選原礦49.8萬(wàn)t相比,其耐磨性提高34%,每付襯板可降低選礦襯板消耗費(fèi)和節(jié)約設(shè)備維簡(jiǎn)費(fèi)共8.58萬(wàn)元,全年可創(chuàng)效益92.3萬(wàn)元。
三門峽富通新能源科技有限公司除了銷售球磨機(jī)外還銷售破碎機(jī)、顎式破碎機(jī)、圓錐破碎機(jī)、顆粒機(jī)等機(jī)械設(shè)備。